Silicone sealing rings are typically constructed using silicone rubber, a synthetic elastomer known for its flexibility, durability, and resistance to temperature extremes, chemicals, and weathering. The construction of silicone sealing rings involves molding or extruding silicone rubber into a ring-shaped structure with specific dimensions and features tailored to the intended application. Here are the key aspects of silicone sealing ring construction and the features that contribute to their effectiveness:
Silicone rubber is chosen for its exceptional sealing properties, including resilience, compression set resistance, and compatibility with a wide range of substances. High-quality silicone formulations ensure consistent performance and longevity in various environments.
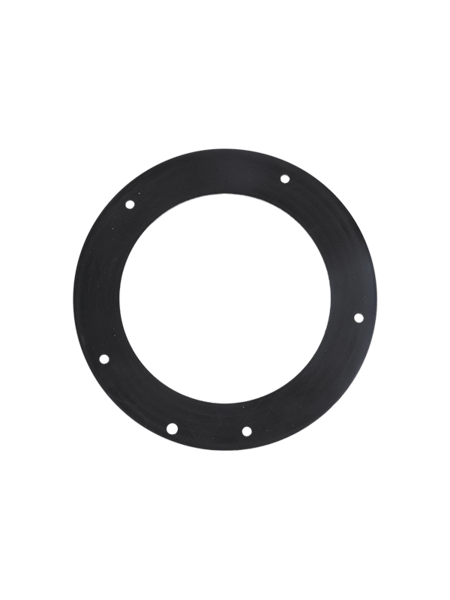
Silicone sealing rings are designed with specific dimensions, profiles, and geometries to achieve a secure and effective seal. Common designs include O-rings, gaskets, and custom-shaped seals tailored to fit specific applications and sealing surfaces.
The cross-sectional shape of silicone sealing rings plays a crucial role in their sealing effectiveness. Rings with round, square, rectangular, or custom-shaped cross-sections are selected based on factors such as sealing pressure, surface irregularities, and sealing requirements.
The surface finish of silicone sealing rings is carefully controlled to ensure smoothness and uniformity, minimizing the risk of leaks or surface imperfections that could compromise the seal. Surface treatments such as polishing or coating may be applied to enhance sealing performance.
The hardness or durometer of silicone sealing rings is selected based on the application requirements, with options ranging from soft and flexible to firm and rigid. The durometer rating indicates the resistance of the silicone rubber to indentation and deformation under pressure, with softer compounds providing better conformability and sealing in low-pressure applications, while harder compounds offer greater durability and resistance to extrusion in high-pressure applications.
Tight tolerance control during manufacturing ensures consistent dimensions and uniformity across silicone sealing rings, facilitating proper fit and alignment with mating surfaces. Precise tolerances help prevent leaks and ensure reliable sealing performance in critical applications.
Silicone sealing rings are engineered to withstand a wide range of temperatures, from extreme cold to high heat, without compromising their sealing effectiveness. Specialized silicone formulations and additives enhance temperature resistance and stability, allowing sealing rings to maintain their integrity and performance in demanding thermal environments.
Silicone sealing rings exhibit excellent resistance to a variety of chemicals, oils, solvents, and fluids encountered in industrial, automotive, aerospace, and other applications. Chemical compatibility testing ensures that silicone sealing rings remain unaffected by exposure to specific substances, preventing degradation or deterioration of the seal over time.
Silicone sealing rings are designed to compress under pressure, conforming to mating surfaces and creating a tight, leak-free seal. The ability of the silicone rubber to deform elastically and recover its original shape after compression ensures long-term sealing integrity and reliability.
The combination of material properties, design considerations, manufacturing techniques, and quality control measures contributes to the effectiveness of silicone sealing rings in providing reliable and long-lasting seals in diverse applications. By selecting the appropriate silicone sealing ring based on specific requirements and operating conditions, users can achieve optimal sealing performance and prevent costly leaks or failures.